
[ad_1]
By Intratec Solutions |
This column is based on “Polypropylene Carbonate Production – Cost Analysis,” a report published by Intratec. It can be found at: www.intratec.us/analysis/polypropylene-carbonate-production-cost.
Polypropylene carbonate (PPC) is a thermoplastic polymer produced from the catalyzed copolymerization of carbon dioxide (CO2) and propylene oxide. The copolymer chain is composed of alternating segments of CO2 and propylene oxide, along with small amounts of propylene oxide homopolymer. Some of its important properties include excellent transparency, good barrier to water and oxygen, printability and nontoxicity.
PPC offers important environmental advantages: it acts as a sequester for CO2, which can help minimize the impact of global warming, and some PPC composites are designated as biodegradable materials.
The process
The present analysis discusses an industrial process for PPC production comprising four major sections: (1) polymerization; (2) phase separation; (3) monomer separation; and (4) pelletizing and finishing (Figure 1).
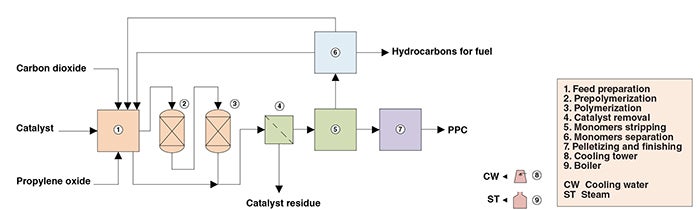
Figure 1. The diagram shows the production of PPC from propylene oxide and CO2
Polymerization. Fresh CO2 feed is mixed with recycled CO2 from the monomers separation stage. Propylene oxide feed is also mixed with a recovered stream. Both reactants are treated for moisture removal. Part of the treated propylene oxide feed is introduced to the polymerization reactor outlet to dissolve the polymer solution obtained in the reactor. The remainder is mixed with catalyst and CO2 feed, forming a liquid solution that is transferred to the prepolymerization reactor. The prepolymerization reaction effluent is fed to the polymerization reactor, where the polymer solution is obtained.
Phase separation. The polymer solution is contacted with a material that binds to the catalyst and allows its removal via filtration. The catalyst-free solution is subjected to gradual pressure decrease, so that unreacted monomers can be released. Once unreacted monomers are removed, the polymer melt is transferred to the pelletizing and finishing stage, while released monomers are routed to the monomers separation area.
Monomer separation. Unreacted monomers are fed to two consecutive distillation columns, from which three streams are obtained. A high-purity propylene oxide stream is recycled to the feed preparation step and mixed with fresh feed. A carbon-dioxide-rich stream (also containing propylene oxide) is also recycled to feed preparation. Another stream, comprising heavy ends generated as side-products, is discharged from the process.
Pelletizing and finishing. The polymer melt is fed to a pelletizing system, where it is homogenized and pelletized. Subsequently, the pellets are packed in bags before being stored in warehouses.
Production pathways
Commercial production of PPC involves the catalyzed copolymerization between carbon dioxide and propylene oxide, in such a way that different manufacturing routes are related to different sources of these raw materials. Figure 2 illustrates PPC production pathways.
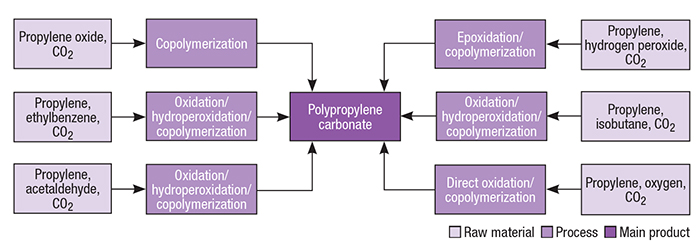
Figure 2. Multiple pathways exist for the production of polypropylene carbonate
Economic performance
The total operating cost (raw materials, utilities, fixed costs and depreciation costs) estimated to produce PPC was about $1,660 per ton of PPC in the third quarter of 2016. The analysis was based on a plant constructed in the U.S. with the capacity to produce 20,000 metric ton per year of PPC.
Edited by Scott Jenkins
Editor’s note: The content for this column is supplied by Intratec Solutions LLC (Houston; www.intratec.us) and edited by Chemical Engineering. The analyses and models presented are prepared on the basis of publicly available and non-confidential information. The content represents the opinions of Intratec only. More information about the methodology for preparing analysis can be found, along with terms of use, at www.intratec.us/che.
[ad_2]
Source link