
[ad_1]
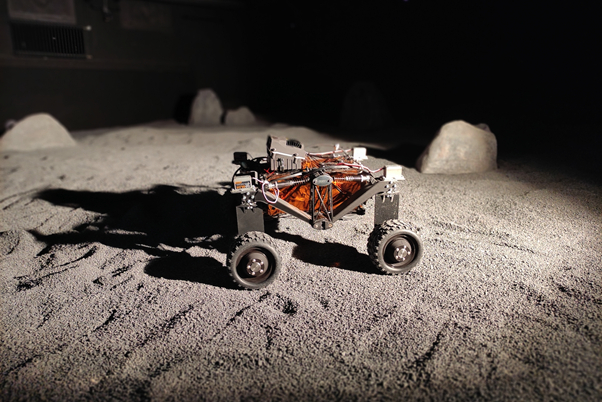
LunaLab rover testing. Photo Credit, all images: Anisoprint
Anisoprint (Esch-sur-Alzette, Luxembourg, U.K.), a manufacturer of continuous fiber 3D printing systems, has used its continuous fiber co-extrusion technology to produce lightweight parts for a lunar rover designed by student team Kepler, winners of ActInSpace 2020, said to be the largest worldwide “hackathon” for the development of new, space-related solutions. The moon rover was tested at the University of Luxembourg’s LunaLab, which has a simulated lunar environment, on Sept. 21, and was exhibited on Sept. 27 (DemoDay).
The Kepler team that developed the rover itself won the “Configure test a DIY lunar rover” challenge portion of the competition, receiving support from experts at the Space Robotics Research Group from SnT and Technoport to explore the business concept and to build the lunar rover on the basis of a prototyped rover configuration. The primary challenge for the team was to make a robot with a mass under four kilograms. With 3D-printed composites an ideal option for lightweight and high strength, the company turned to Anisoprint.
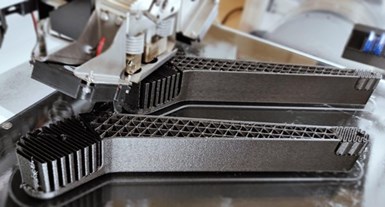
Part in progress using Anisoprint’s Composer A4 printing head.
“Application cases we deal with primarily come from areas where isotropic materials proved ineffective, which means we always change the design for anisotropic reinforcement, both geometry and weight count here,” says Aleksey Ivanov, Anisoprint application engineer. “Composite 3D printing has a large potential for aerospace, and we help people explore it and get maximum benefit from the technology.”
To achieve this weight reduction, two suspension parts — a wheel mount and control arm — were remodeled. Carbon fiber was the chosen reinforcement, and SmoothPA to achieve a polished surface. The resulting part weight is as low as 64 grams for the control arm and 24 grams for the wheel mount (only 15% infill was used).
[ad_2]
Source link