
[ad_1]
The COVID-19 pandemic has necessitated the rapid development of new technologies for vaccine development and delivery. One key development has stemmed from the need for largescale production of mRNA-based vaccines encapsulated in lipid nanoparticles (LNPs), enabling fragile mRNA-based vaccines to better integrate into patients’ cells.
KNAUER has been at the forefront of this vital development in the fight against COVID-19, with the company’s Impingement Jets Mixing technology providing a platform for the high flow production of lipid nanoparticles.
We recently spoke to Dr. Paul Pietsch from KNAUER about the company’s background, its range of specialisms and its pioneering work to facilitate the largescale production of LNPs while meeting the stringent regulations and exacting demands of the biopharmaceutical industry.
Please could you explain what KNAUER can provide to engineers and industry professionals?
KNAUER has been producing high-quality scientific instruments since 1962. We are an experienced partner in the delivery of equipment for use in the pharmaceutical industry, such as liquid chromatography systems and technology for lipid nanoparticle production and encapsulation.
We are proud to have many experts in our team, enabling us to develop innovative and individual solutions designed around each of our customers’ unique challenges. In addition to this, we provide engineering services to develop systems that meet the exact needs and requirements of our end users.
What can KNAUER offer the pharmaceutical industry that its competitors, perhaps, cannot?
There are many companies out there supplying equipment and systems to the pharmaceutical industry, and they come in many shapes and sizes; however, KNAUER still has a unique offering for our partners in the pharmaceutical industry.
Firstly, we are an established company that has been operating for almost 60 years. All of these years of experience mean that we are well versed in providing custom system solutions to our partners.
Secondly, we are neither too big nor too small. Our medium company size means that we can respond flexibly to the needs of our customers – like we did during the coronavirus pandemic with our lipid nanoparticle technology – whilst still having the manpower to deliver solutions at speed.
Our third unique strength is that we produce all of our systems in-house at our headquarters in Berlin. Our on-site production allows us to quickly adapt our existing systems to our customers’ needs using our own CNC production, equipment assembly line and software development team.
For example, if a customer needs a special valve to complete a system that is not available on the market, our construction team can design the required part according to their requirements.
Following design, the part can then be produced by our CNC production and attached to the system. Our software team can then program any functions needed to integrate the valve. This entire process can rapidly be carried out in-house, depending on the time demands of our customers.
To summarize all of this – KNAUER can provide out-of-the-box, custom solutions for the pharmaceutical industry as and when required.
An example of a custom system designed by KNAUER – this system uses 16 pumps for the purification of monoclonal antibodies.
mRNA vaccines have currently been making headlines – how do KNAUER help in their production?
The most suitable delivery format for mRNA-based vaccines is lipid nanoparticles (LNPs). LNPs encapsulate the mRNA used in coronavirus vaccines and the resulting lipid capsule protects the fragile mRNA from degradation, increasing integration into the patient’s cells.
The mRNA encapsulation process uses Impingement Jets Mixing technology, where two streams (one containing lipids and another containing an aqueous solution of mRNA) collide at high velocity in a jet mixing chamber – it is this step that KNAUER’s technology is involved in.
With our expertise in systems engineering and high-pressure dosing, we were able to offer a major pharmaceutical manufacturer the technology they required for the high flow production of lipid nanoparticles.
Our Impingement Jets Mixing Skids have shown outstanding performance in the large-scale production of mRNA encapsulated in lipid nanoparticles for use in coronavirus vaccines. These are now being used globally in similar applications.
Schematic diagram showing the mixing process occurring inside an IJM system.
Are there any breakthroughs or developments that KNAUER is pioneering that you are particularly excited about?
The Impingement Jets Mixing (IJM) Skids we covered in the last question are what excites me most right now.
Before the coronavirus crisis, equipment for the production of LNPs only existed at a laboratory scale, meaning the largescale production of mRNA encapsulated in LNPs was not yet possible.
The coronavirus crisis meant that technology that could be used in the large scale production of mRNA-based vaccines suddenly became urgently important. This posed a challenge as the large scale production of such systems had not yet been undertaken, and the lab-scale production of LNPs was not easily scalable.
To solve this problem, we combined several lab-scale units in parallel to produce our IJM Skids, which could then be used for LNP production at a large scale. This sounds like a simple solution, and, in theory, it is. However, it required a high degree of finetuning and expertise to implement this according to the regulations and demands of the biopharmaceutical industry.
Our existing devices had to be adapted for pharmaceutical production, which included the design of custom manifolds for inlets and outlets, flow path optimization, design adaptation to meet clean room C requirements and the provision of interfaces for our customers’ own PLC systems.
We are proud to have played a role in making history with coronavirus mRNA vaccines, being the first example of the use of mRNA-based LNP vaccines. We’re even more proud to have done all of this under incredible time pressure, helping to deliver a coronavirus vaccine when the world needed it most.
KNAUER’S IJM Skids have played such a crucial role in the production of mRNA coronavirus vaccines in Germany that the German Chancellor herself visited the company in September 2021.
What kinds of projects in the pharmaceutical industry has KNAUER been involved in?
Due to the strict confidentiality required by the biopharmaceutical sector, we can’t name any names. We are, however, excited to be working with one of the biggest providers of mRNA coronavirus vaccines.
Our first project with this partner was one of the most exciting projects for our engineering-to-order service to date. This is because of the time pressure and the fact that the system we were developing had never been produced before.
The urgent need for the production of mRNA vaccines meant that a typical project flow – with planning, engineering, offer and order stages – could not be used. Production began immediately following the first request, whilst our engineers designed the system in parallel to production with our customer.
Due to the fast-moving requirements of the project, we had to remain flexible. Sometimes work we had done one day needed to be reversed or modified the following day. Following three months of highly focused development, we were proud to see the system in production.
It’s important to mention that our offerings for the pharmaceutical industry go beyond our IJM Skids. We also provide complete solutions for the purification of other active pharmaceutical ingredients (APIs).
We are often approached by customers who know their target API and know how to produce it but lack the ability to purify it – this is where KNAUER can help.
When approached by such a customer, we help them from the bottom up. We begin with a column screening, then develop a method and optimize it at the lab scale. Using these results, we can then run the purification using our simulated moving bed (SMB) system, which allows for continuous purification.
Following this scale-up, our customer can then begin producing API at a pilot scale.
How does KNAUER support GMP compliance for pharmaceutical manufacturers?
KNAUER provides expertise and resources to pharmaceutical manufacturers to help them implement GMP-compliant pharmaceutical production. Our customers often have specific requirements for the KNAUER hardware that they are interested in, and these are usually defined in their specific User Requirement Specifications (URS).
We discuss the URS with our customers and help ensure that their regulations remain up to date, helping manufacturers deliver products that meet their end users’ requirements and adhere to all required safety standards.
Our GMP services are based on our hardware and software solutions. Product safety is supported by documentation on product conformity and the compliance of materials used as wetted parts.
Quality control is ensured by installation and operational qualification, as well as performance verification. Furthermore, a factory acceptance test (FAT) and a side acceptance test (SAT) are standard GMP services.
We also place a great emphasis on personal training, including software, hardware, maintenance and service training packages.
Installation and testing of an IJM Skid for the encapsulation of API in lipid nanoparticles
What are some of the new challenges that face the pharmaceutical industry in the wake of the COVID-19 crisis, and how will KNAUER help tackle them?
From the COVID-19 crisis, we have learned to be open to new technologies and that, for us, being fast and flexible are the keys to success.
In a bigger perspective, there is a possibility that the coronavirus crisis has accelerated a great change in the vaccine landscape – a migration to mRNA-based vaccines appears to be on the horizon.
mRNA vaccines have the unique advantage that they can be rapidly modified in response to virus mutations, and this benefit could see them beginning to dominate the field in the coming years.
LNP-encapsulated mRNA technology does not stop there either – we expect to see the technology being used in gene therapy, while LNPs, in general, can be used for the delivery of other fragile APIs. We are at the beginning of a new era in medicine and we’re proud to be at the forefront.
We’re excited to be part of this revolution and look forward to helping drive this medical revolution with our tailor-made solutions for pharmaceutical processing and production.
How does KNAUER intend to work alongside consumers in a post-COVID world?
We intend to work alongside consumers as we did before. For us, close collaboration with our customers is the key to developing products and systems that our customers are truly happy with.
We have a dedicated team of experts from hardware construction to quality experts available throughout the complete design process, and these experts are on hand to support our customers with the expertise they need to find the best solution to their challenges.
About Dr. Paul Pietsch
Dr. Paul Pietsch studied Food Technology at the Anhalt University of Applied Science before going on to complete a chemistry Ph.D. at the Technical University of Berlin. Following completion of his doctorate, Dr. Pietsch joined the team at KNAUER as a product manager for their continuous chromatography systems. After 3 and a half years in this role, he moved on to become the head of engineering solutions across the entire business.
About KNAUER Wissenschaftliche Geräte GmbH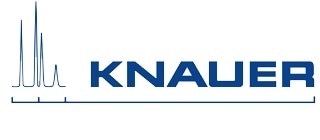
KNAUER Wissenschaftliche Geräte GmbH is a middle-sized company that has been developing, manufacturing and distributing laboratory instruments around the world since 1962.
With more than 130 employees, Knauer is one of the well-established manufacturers of HPLC instruments, SMB systems, and osmometers. Product portfolio includes extremely compact HPLC solutions, UHPLC systems for high-resolution analysis, preparative HPLC instruments, process LC equipment for the purification of substances in the kilogram scale, autosamplers, column thermostats, degassers, detectors, dosing pumps, eluent mixers, flowmeters, LC columns, and accessories and spare parts, amongst others.
The source of Knauer’s success is numerous world’s firsts that have won more than 20 awards for innovation.
[ad_2]
Source link