/https://specials-images.forbesimg.com/imageserve/5f21a6ed5db22b440076529e/0x0.jpg)
[ad_1]
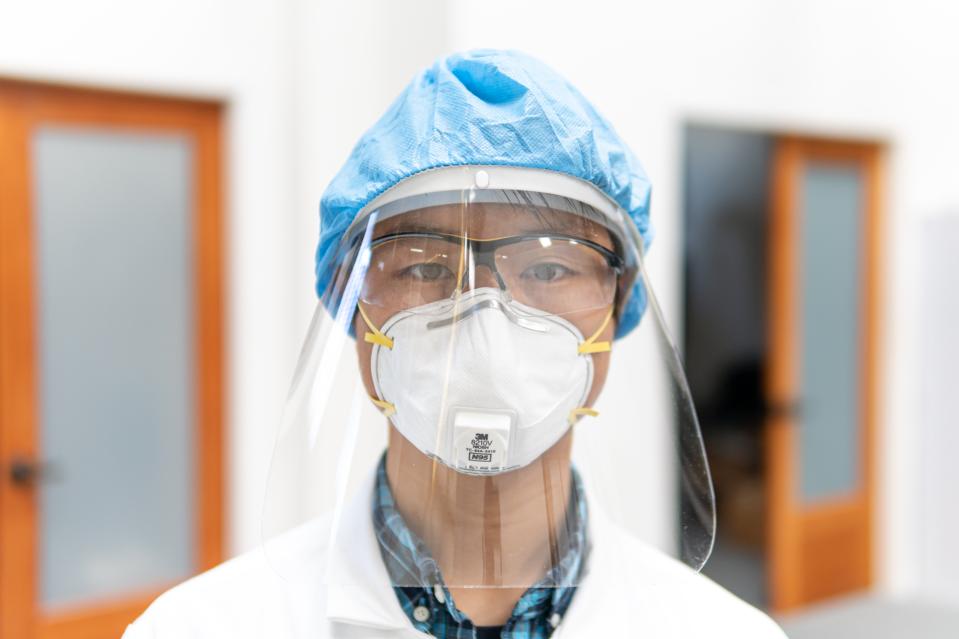
Face shield produced on 3D Systems’ technology to help address the PPE shortage
The coronavirus threw a wet blanket on economic growth the world over, and at least temporarily slammed the brakes on a manufacturing sector that had already been slowing for months. But a silver lining was the remarkable response by manufacturers to the supply chain breakdowns and shortages in the medical products market. Thousands of producers quickly revamped their factories in order to help make critically-needed medical supplies. And if there’s a single technology that was the star of those efforts, it was 3-D printing.
Even before things started getting serious here in the U.S., 3-D printing (also known as additive manufacturing, or AM) was already in use to help deal with the medical crisis brought on by Covid-19. “We saw very early on in northern Italy the lack of medical capacity to deal with the effects,” said Ben Johnson, Director of Product Development, Healthcare, for 3D Systems. “We had our partner there printing valves and splitters to allow the use of a single ventilator for multiple patients.”
Once the crisis reached our shores, use of 3-D printers to respond really took off. “3-D printers were directly involved in so many ways,” Johnson said. “They were used to make complete face shields, face masks, swabs, and ventilator components–and they drove innovative developments of complete new ventilator designs as well. The common response around face shields became a great opportunity for everyone, including hobbyists.”
That immediate response by individual players in every corner of the 3-D printing field was remarkable. So, too, was the cooperation in response to the crisis. “We collaborated with our competitors to ensure understanding of the regulations, validations of materials and products, and exactly what could and couldn’t be printed,” said Johnson. “We worked with them on tech support and materials consulting as well. And we partnered with different consortiums–the National Institutes of Health, the Department of Veterans Affairs, and America Makes [a 3-D printing development public-private partnership], for example.”
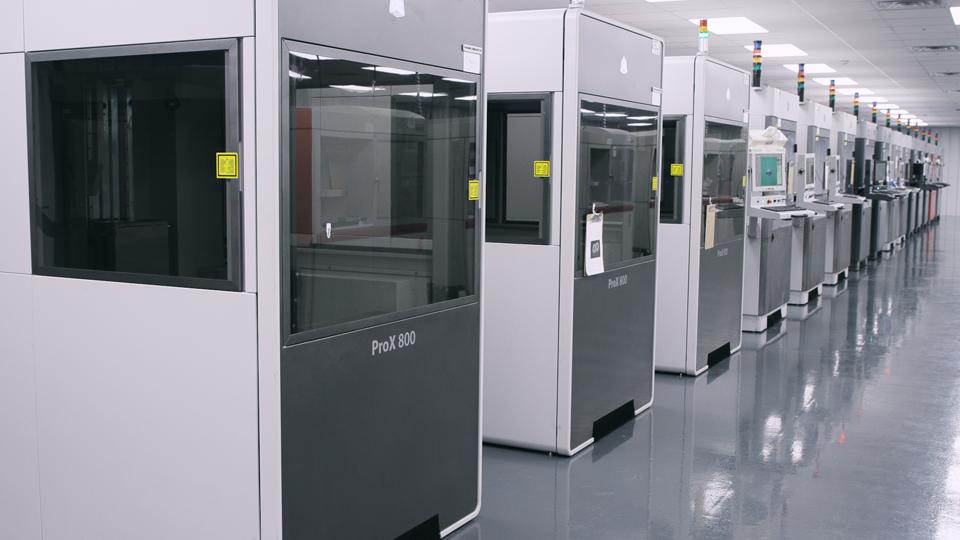
Companies that have considered and planned for additive manufacturing can pivot quickly and … [+]
Now as the world emerges from medical crises and lockdowns, a lot of people are seeing 3-D printing in a whole new light. “There are a few different threads to the trends going into the crisis and coming out of it,” said Ferdie Bruijnen, VP, Supply Chain Operations at 3D Systems. “An Ernst & Young study showed attitudes toward AM had already shifted between 2016 and 2019, with the percentage of companies using AM strategically doubling over that time, from 4% to 8%, and the percentage with no experience with it all falling by more than half, from 76% to 35%. Then Covid highlighted some important benefits of AM, like the fact that it requires no tooling, that it can handle complex geometries, and that it provides a naturally distributed manufacturing base.”
The distributed nature of 3-D printing is a huge advantage as many companies look at alternative sourcing for both parts and products whose availability was hampered by supply chain breakdowns. “AM has an on-demand base, and that lowers the barrier to entry,” Bruijnen said. “The distributed nature of its manufacturing was a big plus during the crisis – Covid really highlighted the value of that.”
Those advantages have put 3-D printing into a strong position as manufacturing recovers. “Bridge manufacturing is a big opportunity,” said Bruijnen. “Rather than a manufacturer having a tool to cover 110% of normal demand, they can have one to cover 95% and use AM to handle flex capacity. AM showed in the pandemic how it offers quick turnaround and flexibility.”
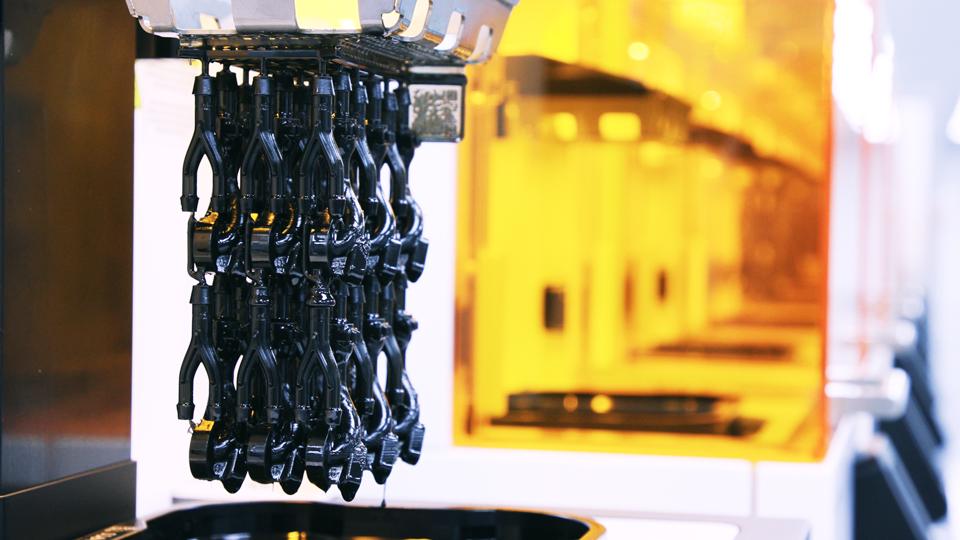
With capabilities such as stacked printing, additive manufacturing enables direct digital production … [+]
The demonstrations of end-use product manufacturing that 3-D printing exhibited over the past few months have changed a lot of minds about the nature of the technology. “AM showed itself to be much more than a prototyping technology,” Bruijnen explained. “In 2009, the market became enamored with AM, with people saying it would replace injection molding. Well, we know that’s never going to be the case. But we also know that it has a proper place in the manufacturing tool set.”
“The coronavirus situation brought to light the capacity of 3-D printing to do rapid response,” said Johnson. “The ventilator splitter is a good example – we saw a 24-hour turnaround on that response. The technology is going to be viewed now as having that kind of potential. It will help democratize production.”
Bruijnen agrees. “The technology has really emerged,” he said. “It was already seen as mature in particular areas – dental, medical, and jewelry, for example, where it had already shown a great match between the technical capabilities and the business needs. But that’s just scratching the surface of its potential. A good example is in cosmetics, where there’s a company that’s printing an advanced-geometry lipstick holder. That better-looking packaging sets it apart from all its competitors. And in general manufacturing, there are a number of areas where it’s imminent that we’ll see the balance tip toward AM taking a chunk of final production.
“AM won’t replace injection molding,” he concluded. “But it doesn’t have to. That never should have been the measure of success.”
[ad_2]
Source link