
[ad_1]
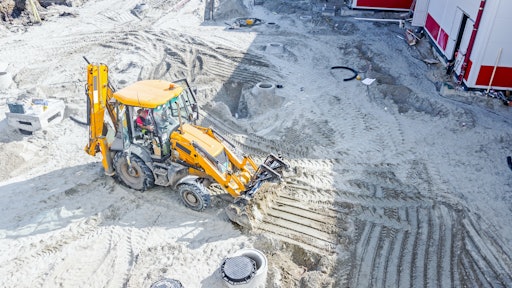
Although the development {industry} has a powerful pipeline of initiatives, particularly infrastructure buildouts, contractors could also be challenged to satisfy demand resulting from a persistent scarcity of staff and excessive turnover.
©Roman_23203 – inventory.adobe.com
We’ve heard the chatter across the water cooler in a post-pandemic office: “No one wants to work anymore.” And while that may not be true, currently the construction industry is short roughly 440,000 workers, according to McKinsey. Contractors should expect this vacuum of talent to continue in 2023. To complete jobs this year and beyond, contractors should consider a multipronged solution.
According to the 2023 Engineering and Construction Industry Outlook, labor has been declining due to an aging population and talent pressures in competing industries. During the past 10 years, workers between 25-54 years old decreased by 8%, and older workers left the industry at an increased frequency. Although the construction industry has a strong pipeline of projects, especially infrastructure buildouts, contractors may be challenged to meet demand due to a persistent shortage of workers and high turnover.
More than inflation, supply chain, or governmental policies and regulations, labor shortages will be the defining challenge of the construction economy for the foreseeable future according to a recent economic forecasts. While we may have to weather the immediate climate, construction companies can attract new talent, maximize operators’ productivity and widen their pool of prospective team members through technology adoption. Discover how four technological solutions can solve labor challenges.
1. Attract, Expand Talent Pool With Semi-autonomous Technology.
Since we were all stuck inside during the pandemic – young and old alike are now factoring in commute time and job flexibility when considering a new opportunity. Contractors now can have answers to other “work from anywhere” jobs with semi autonomous expertise that may be retrofitted to dozers, vans, wheel loaders, and extra. When put in, operators can management a number of machines whereas sitting at a snug remote-control desk.
Operators can activate machines wherever they’re working and begin their day, decreasing journey time to distant or powerful terrain jobs like mining or quarry sites. Reducing commute times and risk of injury appeals to younger generations according to the 2023 Engineering and Construction Industry Outlook.
Tapping into another machine on another job site quickly can improve productivity and help operators to have a better work-life balance. Even if an operator needs help troubleshooting an issue, dealers at the forefront of the industry’s technology innovation offer remote support to access machine software and solve problems in real-time before calling a field tech or traveling to an equipment store.
Also, adding semi autonomous technology to equipment, like skid steers or compact tractor loaders (CTLs), could open operator positions to those who may not have considered this type of work, including people with physical disabilities.
2. Accelerate Expertise With Machine Control.
With baby boomers leaving the workforce, projects may be delayed as recently hired operators learn the ins and outs of specialty projects. Flattening that learning curve is just one advantage of using new technologies. Yes, you read that right – learning new technology is much faster and intuitive than learning old methods. John Deere and other manufacturers have developed machine control technology to help operators onboard faster while also improving smoothness and accuracy.
Grade management advancements include developing global navigation satellite system (GNSS) receivers to help operators visualize where the machine is relative to the grade, allowing precision grading superior to what used to be considered an acceptable tolerance.
Operators have shared success stories with grad management advancements. In fact, I’ve heard stories of how a new hire can learn how to use the machine in a day and a half as opposed to one week without this technology.
For excavators, correct horizontal and vertical positioning the place the machine controls growth and bucket actions to a exact design goal, can increase manufacturing by 30%, permitting the operator to concentrate on controlling the arm perform whereas the system raises and lowers the growth to take care of grade.
[adinserter block=”4″]
[ad_2]
Source link