
[ad_1]
An executive and entrepreneur who designed battery packs for SpaceX has partnered with a leader of India’s transportation industry in a venture designed to improve the lifecycle of lithium-ion batteries, and help that country’s transition toward electric passenger vehicles.
Porter Harris, a battery engineer known for his work in thermal cooling and heating methodology, and Pankaj Dubey, who made his mark in bringing all-terrain vehicles and snow scooters to India, on Sept. 28 announced their Power.Global venture has agreements with stationary storage integrator PositivEnergy and battery recycling processor Redivivus in support of Power.Global’s effort to upgrade battery technology.
Power.Global, formed in 2019, designs high-performance clean energy and mobility products. The company in a news release Tuesday said the company “is building toward a fully sustainable and equitable battery economy through strategic partnerships, responsible manufacturing practices and product lifecycle management.”
“To help alleviate some of the stress on global supply chains, we’re developing in-country battery manufacturing in India, the U.S. and other global markets, and working with local cell manufacturers to develop our 100% made-in-country electric battery module,” Harris told POWER. “Bringing production onshore to local markets will not only boost local economies but also mitigate potential supply chain disruptions. Additionally, we have an R&D lab and in-house cell testing to allow us to test and validate cells from other manufacturers in the market and expand and diversify our supply chain to eliminate disruptions. Our team in India is specialized in supply chain and distribution to support an efficient network in-country, from sourcing and procurement to sales and distribution.”
Battery Design Experience
Harris, who also co-founded Romeo Power Technology and was chief battery engineer at Faraday Future, has plenty of experience in battery design for electric vehicles (EVs). He was the lead engineer of the SpaceX group that designed battery packs for that company’s Falcon 9, Cargo Dragon, and Crew Dragon vehicles. He then joined several former Tesla engineers at Faraday Future as senior manager for battery hardware engineering.
At Romeo Power, also staffed by engineers from Tesla and SpaceX, Harris and his team were focused on the design and manufacturing of lithium-ion batteries for medium short-haul and heavy-duty long-haul trucks, specialty trucks, and buses.
“We’ve gathered a lot of good momentum, and this is just the start of our journey,” said Harris of Power.Global’s current work. “By applying the lessons learned from developing energy storage solutions over the last few decades, and creating strategic partnerships with industry innovators, we’re better equipped in the long run to mindfully and responsibly create a sustainable and circular battery value chain.”
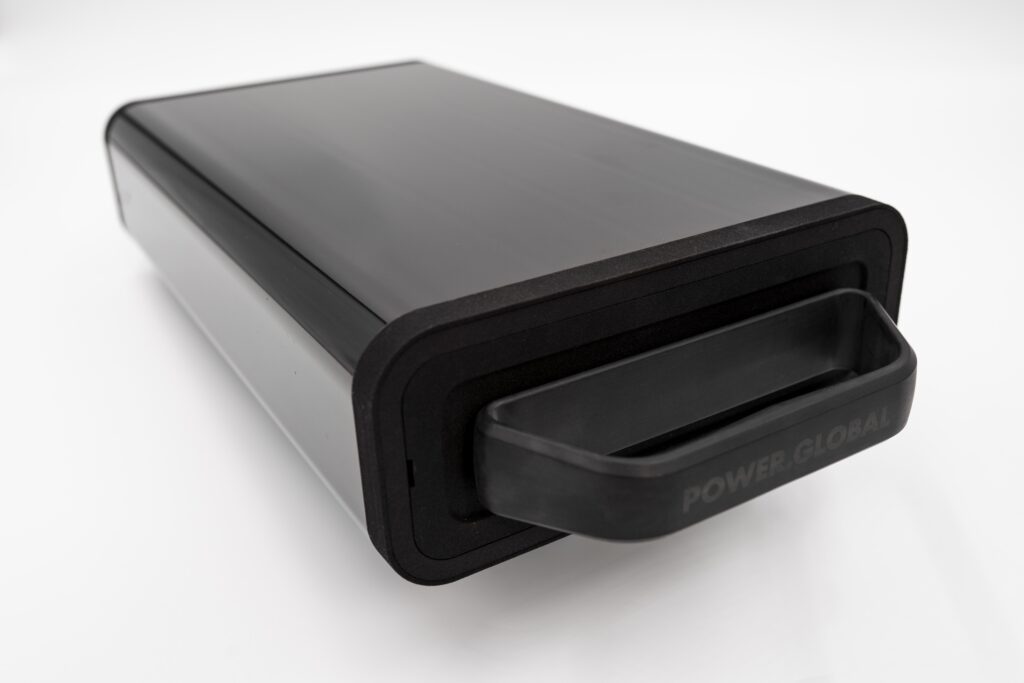
Harris told POWER that Power.Global’s flagship product, the eZee battery module (Figure 1), “is the foundation for which all of our upcoming product lines and partnerships will be built upon, both in India and in other global markets. In addition to electrifying rickshaws, Power.Global will be partnering with OEMs [original equipment manufacturers] to provide our swappable eZee battery for other modern applications including light mobility, utility vehicles and robotics.” Harris said the battery’s design draws upon his previous experience, including with SpaceX.
“In regions like India, most electrified three-wheelers are powered by lead-acid batteries, or lithium-ion batteries imported from China,” he said. “Power.Global is providing an affordable solution specifically engineered for the sometimes harsh environment of India. Our battery is more energy dense, lightweight and safer than other batteries on the market, designed to be cell runaway fault tolerant and reliable, utilizing technologies previously only seen in space or aerospace applications.”
Supply Chain Gaps
Dubey, former head of Polaris India—where his focus was on lithium-ion battery modules for two- and three-wheeled vehicles—became CEO of Power.Global India in September 2020.
“Despite the significant benefits lithium-ion batteries have over incumbent energy sources like internal combustion engines or lead-acid, there are key gaps in the supply chain—namely lifecycle and recycling—that are only now being addressed in the early markets in developed nations,” said Dubey. “Our goal was to bake those aspects into our strategy from the beginning so that countries like India, which are now on the path to electrification, have a chance to leapfrog those challenges and advance quickly and more sustainably.”
Harris said the battery will have a role in energy storage projects, beyond its use in EVs.
“Once the batteries have reached end of life for their original applications, they will be used for stationary energy storage in second-life microgrid applications. These batteries will be tied-in with solar panels to provide energy to rural areas that do not have reliable access to energy, which could be domestically in the U.S. or abroad,” he said. “After the batteries have been completely depleted of all useful life, Power.Global has just inked a partnership with Redivivus, a battery recycling processor, to reclaim up to 92% of materials, while recirculating and reprocessing chemical reagents for direct reuse in the material supply chain.”
Energy as a Service
The eZee modules are the key part of Power.Global’s Energy-as-a-Service (EaaS) program, which will provide battery swap kiosks at select locations throughout India. The program also will allow Power.Global to oversee the battery lifecycle from application to second life across India’s EV sector.
“Whether we’re talking rockets or e-rickshaws, sustainable electrification requires durable, high-performing batteries and energy storage,” said Harris. “At SpaceX, I spent a number of years leading a team for the battery engineering and life support systems, eventually pioneering the battery development for the Dragon spacecraft and Falcon 9 rocket. Since then, I decided to bring my focus back down to Earth to cater to the larger 90% of the global population that are in need of clean energy solutions. Funny story: I actually sold all of my SpaceX stock to self-fund Power.Global.”
He continued: “The idea behind Power.Global is to bring these newer technologies that we developed for spacecraft and performance electric vehicles to emerging markets to help clean up the transportation sector, predominantly 2-stroke, 4-stroke and diesel engines, which produce heavy pollution.”
Power.Global also Tuesday announced it has partnered with PositivEnergy, a Miami, Florida-based renewable energy solutions company that provides end-to-end system design and service for commercial energy storage and EV charging infrastructure. The companies will develop stationary storage solutions that support projected grid demand from electrification, with an eye toward facilitating the transition to renewable energy in global markets.
The stationary storage solution, built upon Power.Global’s scalable battery technology, is expected to achieve a 15-to-20-year product lifespan, according to the company.
“PositivEnergy simplifies the process of deploying best-in-class energy systems. It’s the right time to think not just about how we accelerate electrification, but also how we do it sustainably. Power.Global’s module is a major step forward and Redivivus is an important part of the sustainability solution,” said Ed Wise, founder and CEO at PositivEnergy.
No-Burn, Hybrid Recycling Process
Redivivus is a battery recycling processor. The companies in Tuesday’s announcement said that once Power.Global’s EV and stationary storage battery modules reach their end of life, Redivivus will reclaim up to 92% of materials (Figure 2), as Harris noted, while recirculating and reprocessing chemical reagents for direct reuse in the recycling process.
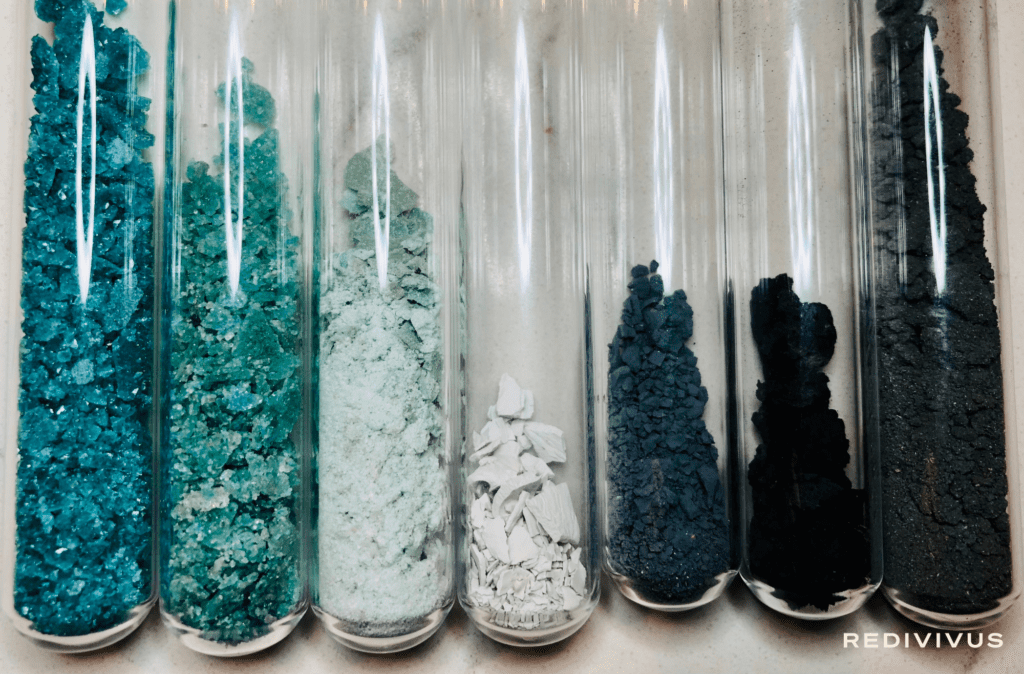
Redivivus, headquartered in Colorado Springs, Colorado, uses a no-burn, hybrid process for battery recycling; current lithium-ion battery recycling processes usually require high-temperature melting-and-extraction or single-use chemical processes, generating significant waste. Redivivus has said its Redi-Cycle technology recovers battery materials for secondary markets, reducing the reliance on metal mining. The company said it will offer mobile Redi-Shred recycling units (Figure 3) for Power.Global service and sales centers throughout India, and build recycling lines at Power.Global’s factories in Pasadena, California, and Greater Noida, India.
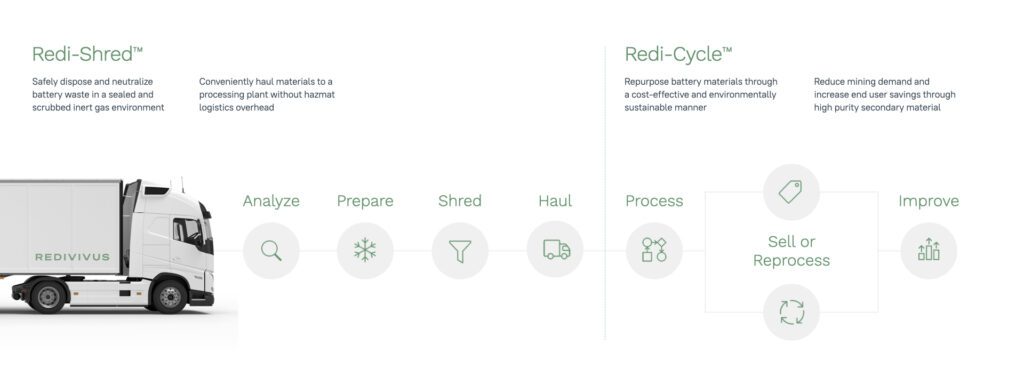
“Our white-glove recycling process brings peace of mind to battery manufacturers knowing their hard work and materials will have a new life, reducing overall carbon footprint,” said Erika Guerrero, co-founder and CEO at Redivivus. “Recycling starts with manufacturing safe, quality battery products. Partnering with Power.Global gives us confidence that adoption of recycling is being thought through from design conception.”
—Darrell Proctor is a senior associate editor for POWER (@POWERmagazine).
[ad_2]
Source link